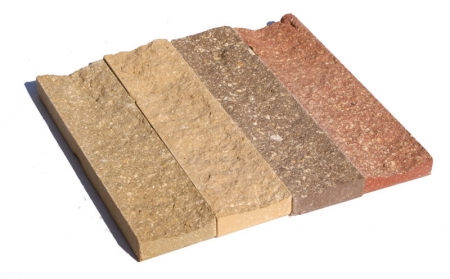
Используемое сырьё:
В качестве сырья для лицевого гиперпрессованного кирпича используют отсевы твёрдых камней, которые остаются после разработки карьеров.
Мы используем только экологически чистую технология, после которой не остаётся отходов, ни жидких, ни твёрдых, ни газообразных.
Дозировка компонентов:
Компоненты, входящие в прессуемую смесь:
- Заполнитель, получаемый отсевом из дробления известкового щебня, от 85 до 92%
- Вяжущее вещество. Это портландцемент, составляющий от 8 до 15% общей массы смеси. Пример: марка ПЦ 500
- Железоокислый пигмент для окрашивания. Применяются также другие пигменты, составляющие от 2 до 7% общей массы прессуемой смеси.
Заполнитель загружают фронтальным погрузчиком или грейфером из оперативного склада в расходный бункер отсева. Вяжущие компоненты поставляют в цементный приёмный бункер.
Процесс дозирования начинается, когда оператор нажимает пусковую кнопку на весовом контроллере. Материал подаётся в передвижной контейнер, стоящий на весовой платформе. Электронный весовой терминал контролирует точность дозирования. Отклонения составляют +-0.5% от массы каждого компонента. Дозирование пигмента происходит точно таким же. После завершения процесса дозирования индикатор показывает вес каждого компонента. Оператор в любое время может контролировать вес и сравнить его с запрограммированной величиной.
Во время дозирования отсев проходит через вибрационное сито, которое находится между ленточным питателем и бункером. В это время отсеиваются крупные фракции сырья.
Смешивание и дробление:
Смесь после дозирования попадает в смеситель-дробилку. Там происходит смешивание, дробление и активизация полученной смеси. Чтобы получить качественный кирпич, необходимо самое тщательное смешивание. Чтобы обеспечить высокую степень гомогенности смеси, которая в свою очередь влияет на прочность, качество цвета и водопоглащательную способность смеси, используют скоростной ротор, скорость вращения которого достигает 1480 оборотов в минуту. Готовая смесь направляется в приёмный бункер пресса.
Формование изделий:
Для получения фасадного кирпича высокого качества нужен контроль давления и высоты изделия-сырца. Это автоматический процесс с контролем качества изделия. При малейшем несоответствии контроллер останавливает производство и брак отправляется в в смеситель-дробилку. Также заданные параметры можно изменять, не останавливая процесс производства.
Пропаривание:
Свежие изделия на укладочных поддонах пропариваются в камерах при температуре 40-70С в течении 8-10ч. После пропарки кирпич отправляют на стройплощадку на транспортных поддонах. Окончательную прочность кирпич набирает уже в кладке в течении 30-ти дней.